A Record of Metal & Flame
How to Choose a Plasma Cutter
Plasma cutters are highly effective tools for metal fabrication, delivering clean, precise cuts with speed and reliability. Choosing the right plasma cutter involves considering several key factors. First, assess the type and thickness of the material you’ll be cutting most often. Thicker materials require higher amperage plasma cutters, while thinner materials can be cut with lower amperage.
Second, determine the input power requirements. Plasma cutters come in options for 115V, 230V, or dual voltage. Hobbyists may find 115V suitable for light-duty work, while 230V machines provide the power needed for professional-grade projects. Dual voltage cutters offer flexibility for different environments.
Third, evaluate the duty cycle, which indicates how long the machine can run before needing a cooldown. High duty cycles are ideal for heavy, consistent use, while lower duty cycles are sufficient for smaller jobs. Portability is another consideration—lightweight models are great for mobility, whereas larger, stationary machines may offer more features.
Lastly, factor in operating costs, including consumables like nozzles and electrodes, which vary in durability and efficiency across brands.
It should be noted that this guide is not a replacement for in-person instruction—you should always seek instruction from a qualified trainer. However, here are five key things to think about when choosing the plasma cutter that best suits your needs.
Plasma Cutter Material Thickness and Amperage
The first thing you need to know is the type and thickness of the material you’ll cut most often. Plasma cutters can handle conductive metals like steel, stainless steel, aluminum, and copper. However, the thickness of the material has a direct impact on choosing the right plasma cutter, since different projects require different amperages.Amperage is crucial when it comes to cutting thicker materials. For example, lighter projects on thinner materials will require less amperage, while heavier fabrication work on thicker metal will demand a plasma cutter with higher amperage.
If your plasma cutter doesn’t have enough power, it may struggle to cut through the material, slow you down, and make your projects more difficult, not to mention the subpar cut quality. Be sure to choose a machine that properly matches the material and thickness requirements of your most common tasks.
Plasma Cutter Input Power
Another important factor to consider is the required input power of the machine. Plasma cutters are typically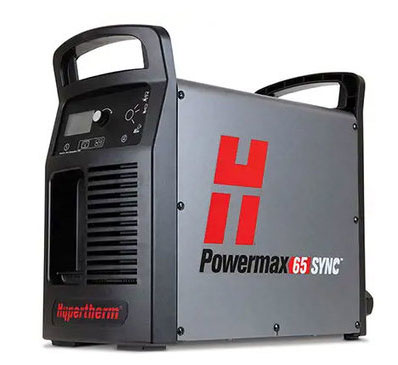
115V Plasma Cutters:
These are often suitable for beginners or those working out of standard home outlets. They’re great for hobbyists or light-duty work but may lack the power needed for large-scale or professional projects.
Dual Voltage Plasma Cutters:
These are ideal for users who frequently move their machine between different locations and need flexibility with power sources. Dual voltage plasma cutters can adapt to both 115V and 230V outlets, making them a versatile option.
230V (or higher) Plasma Cutters
If you’re looking for more cutting power for heavier jobs, a larger system will require 230V input power or higher. These machines are suitable for professional environments cutting thick materials with high-throughput requirements. Think about where you’ll be using your plasma cutter and decide what your priorities are: portability, flexibility, or high output.
Plasma Cutter Duty Cycle
The duty cycle is a measurement of how long a plasma cutter can operate continuously before it needs to cool down. It’s typically expressed as the amount of time the machine can be operated within a 10-minute period. For example, if a plasma cutter has a 40% duty cycle, it can operate for four minutes out of every 10 and then needs a six-minute cooldown.Long Duty Cycles:
Plasma cutters with higher duty cycles are best for heavy-duty fabrication and high-speed production environments where consistent use is required.
Short Duty Cycles:
If you only need a cutter for occasional use or smaller jobs, a shorter duty cycle may be sufficient. Choosing a plasma cutter with the appropriate duty cycle is important to avoid interruptions in your workflow. If your operation is focused on large-scale production, you’ll want a machine with a high-duty cycle that can keep up with your pace.
Plasma Cutter Portability
Ask yourself whether portability is important to your work. If you’re planning to keep the cutter in one place, a larger machine could be a better option since it often comes with more features and cutting capability. However, if your projects require mobility, look for lighter, portable models that are easier to carry.
Plasma Cutter Operating Costs
Beyond the upfront cost of purchasing a plasma cutter, think about its long-term operating costs. Plasma cutters use consumables such as shields, nozzles, and electrodes to perform their cuts, which wear down over time and need to be replaced. The consumption rate of these components varies from one cutter to another. Some machines and brands are more efficient than others with consumables lasting longer between replacements. Additionally, while cheaper consumables may seem like a good deal, investing in OEM consumables may help you save money over time by reducing how often parts need to be replaced.
Research both the plasma cutter itself and the consumables it uses. This will help you calculate the total cost of ownership and help you find a machine that balances performance and affordability.
Why Plasma Cutting Is a Smart Investment
When it comes time to choose a plasma cutter, keep these factors in mind: material thickness, input power requirements, duty cycle, portability, and operating costs. By clarifying your specific needs, you’ll be able to find a machine that fits your projects and helps you work more effectively.
Need Help Selecting a Plasma Cutter?
Finding the right plasma cutter might seem overwhelming, but WeldingSupply.com is here to help make the process easier. We offer a wide range of plasma cutters, tools, and consumables to meet your needs—whether you’re a hobbyist, contractor, or professional fabricator.Our experienced team can help answer your questions and guide you toward the best options for your setup. From lightweight portable units to industrial-grade machines, we have solutions for every application.
Browse our plasma cutting products online or contact us for advice on making the right purchase. WeldingSupply.com is dedicated to helping you work faster, smarter, and more efficiently with tools that get the job done right. Reach out today to learn more!