ALL ORDERS $9.99 FLAT RATE SHIPPING
A Record of Metal & Flame
The History of Welding
Mar 18, 2025
Summary: Welding has a long history. It began with forge welding in Ancient Egypt and has evolved into today’s high-tech, automated methods. Innovations like arc welding, oxy-acetylene welding, and robotic welding have changed industries. They impact shipbuilding, aerospace, and automotive manufacturing. New technologies like TIG, laser welding, and electron beam welding offer high precision and efficiency. Also, smart tech and AI are set to change the future of the industry.
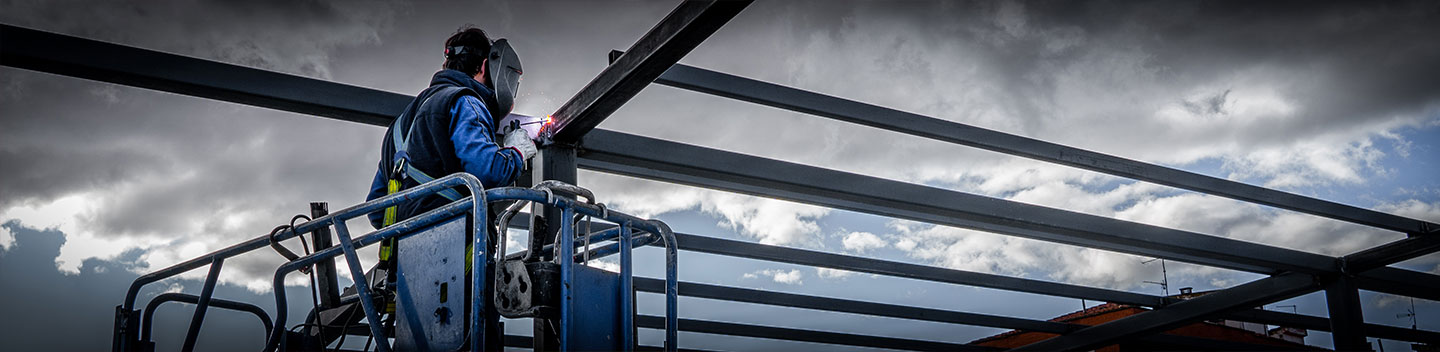
1. When Did Welding Begin?
Welding is key in today's world. It helps build everything from skyscrapers and ships to airplanes and new medical technology. Welding has greatly influenced humanity. Its impact reaches far into the past and over centuries, this process has evolved. It highlights our endless quest for innovation and progress. Welding has a rich history. By looking at its origins, key milestones, and modern advancements, we see how this craft has influenced society for thousands of years.
Welding began during the Bronze Age, around 3,000 BC. This was when forge welding was invented, and it is the first known method for joining metals. In Ancient Egypt, metalworkers found that heating two metal pieces made them malleable. Then, they could hammer or press them together to form a strong bond. This process was used to create tools, weapons, and decorative items.
Historical artifacts point to the sophistication of these early techniques. Examples include lap joints in circular gold boxes from about 2,000 years ago. There were also forged jewelry, eating utensils, and swords. By 600 AD, blacksmiths had discovered how to turn iron into steel, marking a significant leap in metallurgy. Steel swords were strong and sharp, making them very valuable. The techniques created during this time set the stage for future metalworking advancements.
In the Middle Ages (500 AD-1500 AD), metalworking, including welding, saw major advancements thanks to technology. Water-powered hammers were introduced, which simplified the labor-intensive aspects of forge welding. At the same time, craftsmen began experimenting with different alloys to expand the range of materials that could be joined.
The field was further advanced in the Renaissance. In 1540, Italian metallurgist Vannoccio Biringuccio published De la Pirotechnia. This was the first printed book focused on metallurgy. Meanwhile, great minds like Leonardo da Vinci shared sketches and ideas on welding concepts. Despite these breakthroughs, welding during this era remained a predominantly manual, labor-intensive process.
Fast-forward to the 19th century, the Industrial Revolution served as a catalyst for major leaps in welding. Inventors looked for faster ways to join metals. The growing need for quick manufacturing pushed them to find better methods.
In 1800, Sir Humphry Davy discovered the electric arc. This discovery led to arc welding, a method that changed the industry forever. Soon after, his cousin Edmund Davy discovered acetylene gas in 1836. This discovery helped shape the future of gas welding.
The development of arc welding during the late 19th century introduced a new era in metal fabrication. In 1881, Nikolai Benardos and Stanislav Olszewski patented the first practical application for arc welding. They developed a carbon electrode process to weld lead plates for storage batteries. They called the welding process, “Electrogefest”, meaning electric god of fire. The idea of using an electric arc to join metals caught on quickly. It spread through Europe and the United States, laying the groundwork for future developments in welding.
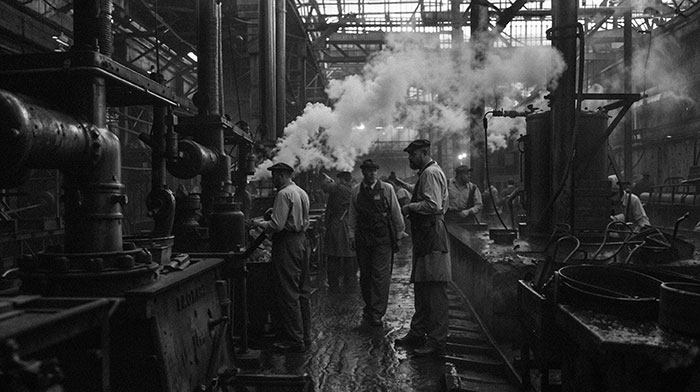
While arc welding was making waves in the late 19th century, another welding method emerged—oxy-acetylene welding. French engineers Edmond Fouché and Charles Picard invented a process in 1903. They combined acetylene gas and oxygen which created a flame that was hot enough to melt and join metals.
Oxy-acetylene welding quickly became popular. Its portability and precision attracted many industries, like shipbuilding, automotive, and construction. Its impact shaped later gas welding methods, making it a key part of early 20th-century welding.
The First World War (1914-1918) created an urgent need for faster, more adaptable production technologies. Welding became essential for building military ships, tanks, and weapons. It led to major advancements.
During this time, Oscar Kjellberg and P.O. Nobel helped create the welding technology we use today. Kjellberg invented the flux-coated electrode. This protected the weld puddle from air and helped make welds stronger.
This invention became the foundation for Shielded Metal Arc Welding (SMAW). Nobel improved welding equipment, making the process safer and easier to use in factories and projects. Their work made welding reliable and changed manufacturing and construction forever. In 1919, groups like the American Welding Society (AWS) were established. They aimed to boost research, teamwork, and education to speed up welding progress.
During World War II (1939-1945), welding became much more common. This change happened because global industrial production grew to meet wartime needs. Applications ranged from shipbuilding to aircraft manufacturing. To enhance production speeds, submerged arc welding (SAW), invented in the 1930s, became widely used. SAW protected the weld with granular flux, helping to improve quality and efficiency on very thick welds.
Also, during this time, stud welding and resistance welding improved. This was especially true in shipyards and factories making military equipment. The war's focus on innovation helped to push welding technology to unprecedented levels.
During this time, welders began using shielding gases like helium and argon. These gases helped keep the molten weld pools safe from contamination. They also improved the quality of the welds. TIG and MIG welding became popular in industries that needed high-quality welds like aerospace and automotive manufacturing.
Automation made assembly lines more efficient, especially in the automotive industry. Robotic welding changed how car panels, chassis, and structural components are made.
In the 21st century, the welding industry has adopted advanced technologies. Laser welding and electron beam welding (EBW) are key examples. Laser welding is now common in industries that need high precision. This includes aerospace, electronics, and medical device manufacturing. Its ability to create strong welds with little heat distortion makes it great for joining delicate parts.
EBW can also weld materials with high melting points, like titanium and superalloys. This makes it essential for important uses, such as jet engines and spacecraft.
New welding techniques aim to be eco-friendly and researchers are working to cut energy use and make resource use more efficient.
WeldingSupply.com is dedicated to offering the latest welding products. As technology advances, we ensure that fabricators around the world can access the next chapter of welding history. Welding has a long history and remains vital today. Whether using old techniques or new technologies, it plays a key role in shaping the future.
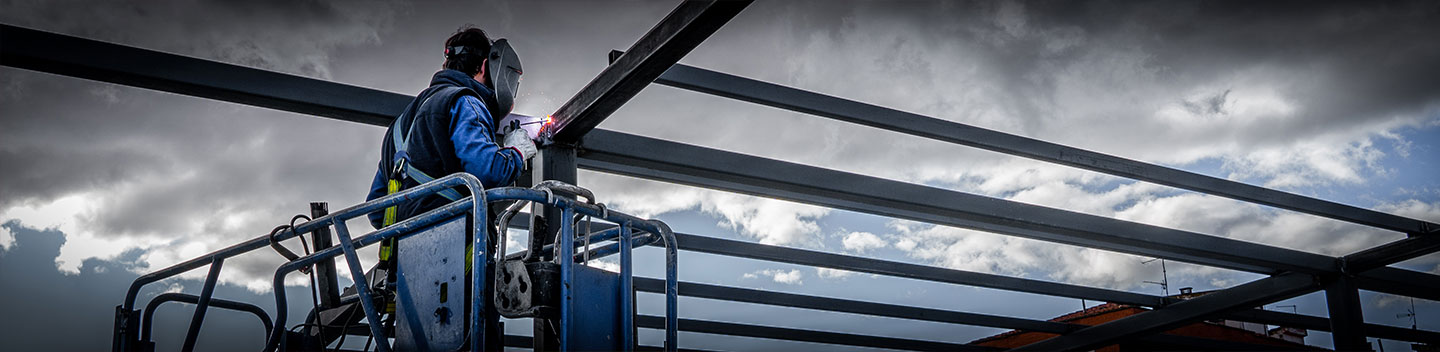
1. When Did Welding Begin?
2. The Middle Ages and the Renaissance: A Period of Refinement
3. The Industrial Revolution: Enter Arc Welding
4. The Birth of Oxy-Acetylene Welding
5. Welding Advancements During World War I
6. World War II and Submerged Arc Welding
7. Post-War Advancements in TIG Welding and Plasma Arc Welding
8. Automation and Robotics in Welding (1960s Onward)
9. Modern Welding: Laser Welding, Electron Beam Welding, and Beyond
10. The Future of Welding
Welding is key in today's world. It helps build everything from skyscrapers and ships to airplanes and new medical technology. Welding has greatly influenced humanity. Its impact reaches far into the past and over centuries, this process has evolved. It highlights our endless quest for innovation and progress. Welding has a rich history. By looking at its origins, key milestones, and modern advancements, we see how this craft has influenced society for thousands of years.
When Did Welding Begin?
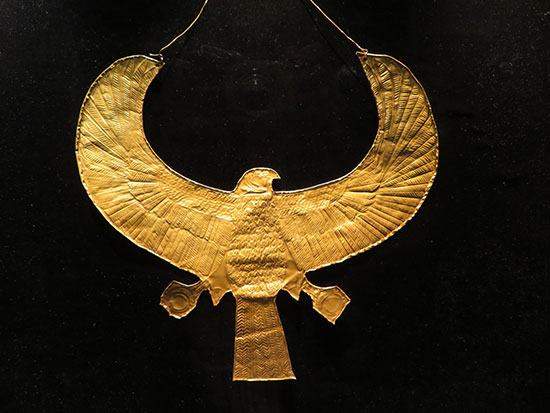
Historical artifacts point to the sophistication of these early techniques. Examples include lap joints in circular gold boxes from about 2,000 years ago. There were also forged jewelry, eating utensils, and swords. By 600 AD, blacksmiths had discovered how to turn iron into steel, marking a significant leap in metallurgy. Steel swords were strong and sharp, making them very valuable. The techniques created during this time set the stage for future metalworking advancements.
The Middle Ages and the Renaissance: A Period of Refinement
In the Middle Ages (500 AD-1500 AD), metalworking, including welding, saw major advancements thanks to technology. Water-powered hammers were introduced, which simplified the labor-intensive aspects of forge welding. At the same time, craftsmen began experimenting with different alloys to expand the range of materials that could be joined.
The field was further advanced in the Renaissance. In 1540, Italian metallurgist Vannoccio Biringuccio published De la Pirotechnia. This was the first printed book focused on metallurgy. Meanwhile, great minds like Leonardo da Vinci shared sketches and ideas on welding concepts. Despite these breakthroughs, welding during this era remained a predominantly manual, labor-intensive process.
The Industrial Revolution: Enter Arc Welding
Fast-forward to the 19th century, the Industrial Revolution served as a catalyst for major leaps in welding. Inventors looked for faster ways to join metals. The growing need for quick manufacturing pushed them to find better methods.
In 1800, Sir Humphry Davy discovered the electric arc. This discovery led to arc welding, a method that changed the industry forever. Soon after, his cousin Edmund Davy discovered acetylene gas in 1836. This discovery helped shape the future of gas welding.
The development of arc welding during the late 19th century introduced a new era in metal fabrication. In 1881, Nikolai Benardos and Stanislav Olszewski patented the first practical application for arc welding. They developed a carbon electrode process to weld lead plates for storage batteries. They called the welding process, “Electrogefest”, meaning electric god of fire. The idea of using an electric arc to join metals caught on quickly. It spread through Europe and the United States, laying the groundwork for future developments in welding.
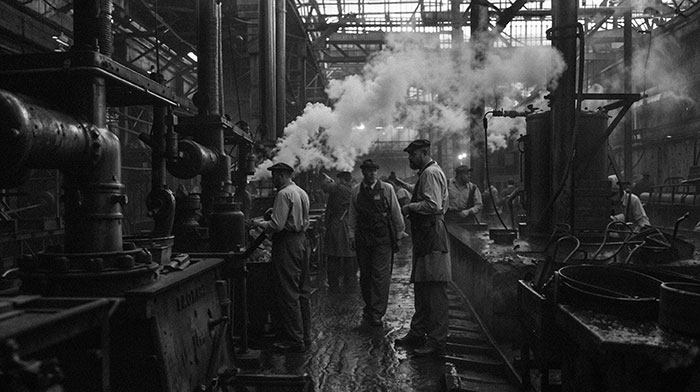
The Birth of Oxy-Acetylene Welding
While arc welding was making waves in the late 19th century, another welding method emerged—oxy-acetylene welding. French engineers Edmond Fouché and Charles Picard invented a process in 1903. They combined acetylene gas and oxygen which created a flame that was hot enough to melt and join metals.
Oxy-acetylene welding quickly became popular. Its portability and precision attracted many industries, like shipbuilding, automotive, and construction. Its impact shaped later gas welding methods, making it a key part of early 20th-century welding.
Welding Advancements During World War I
The First World War (1914-1918) created an urgent need for faster, more adaptable production technologies. Welding became essential for building military ships, tanks, and weapons. It led to major advancements.
During this time, Oscar Kjellberg and P.O. Nobel helped create the welding technology we use today. Kjellberg invented the flux-coated electrode. This protected the weld puddle from air and helped make welds stronger.
This invention became the foundation for Shielded Metal Arc Welding (SMAW). Nobel improved welding equipment, making the process safer and easier to use in factories and projects. Their work made welding reliable and changed manufacturing and construction forever. In 1919, groups like the American Welding Society (AWS) were established. They aimed to boost research, teamwork, and education to speed up welding progress.
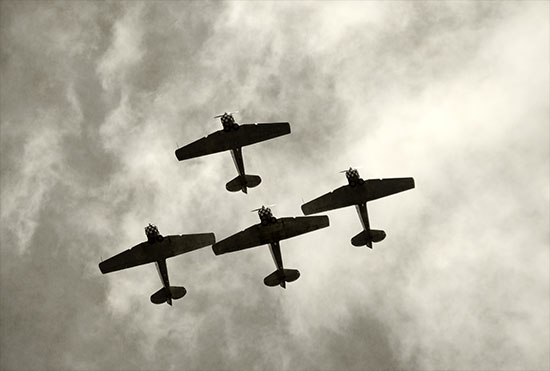
World War II and Submerged Arc Welding
The interwar years brought new ideas, like Gas Metal Arc Welding (GMAW). General Electric introduced it in 1948 for welding aluminum and other non-ferrous materials. This technique utilized a continuously fed wire and enabled fast, efficient welds.During World War II (1939-1945), welding became much more common. This change happened because global industrial production grew to meet wartime needs. Applications ranged from shipbuilding to aircraft manufacturing. To enhance production speeds, submerged arc welding (SAW), invented in the 1930s, became widely used. SAW protected the weld with granular flux, helping to improve quality and efficiency on very thick welds.
Also, during this time, stud welding and resistance welding improved. This was especially true in shipyards and factories making military equipment. The war's focus on innovation helped to push welding technology to unprecedented levels.
Post-War Advancements in TIG Welding and Plasma Arc Welding
After the war, TIG welding (Tungsten Inert Gas), or heliarc welding, emerged. It met the demand for precise, high-quality welding of non-ferrous metals like aluminum. In the 1950s, new methods emerged. GMAW welding with CO2 allowed for faster, hotter welds. Plasma arc welding (PAW) also boosted welding capabilities.During this time, welders began using shielding gases like helium and argon. These gases helped keep the molten weld pools safe from contamination. They also improved the quality of the welds. TIG and MIG welding became popular in industries that needed high-quality welds like aerospace and automotive manufacturing.
Automation and Robotics in Welding (1960s Onward)
The introduction of automating welding processes marked a major turning point in the 1960s. Robotic welding systems were developed to handle repetitive, high-volume tasks with precision. Manufacturers boosted productivity by using robotics with programmable controllers and sensors. This level of efficiency wouldn't be possible with manual labor alone.Automation made assembly lines more efficient, especially in the automotive industry. Robotic welding changed how car panels, chassis, and structural components are made.
Modern Welding: Laser Welding, Electron Beam Welding, and Beyond
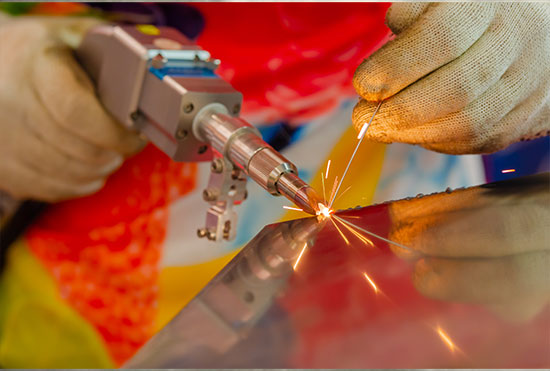
EBW can also weld materials with high melting points, like titanium and superalloys. This makes it essential for important uses, such as jet engines and spacecraft.
The Future of Welding
While welding has come a long way, the future holds even greater promise. AI and machine learning are changing the industry. They allow systems to watch welding parameters in real-time. They can also predict when maintenance is needed and make adjustments while welding. Smart technologies are part of Industry 4.0. They create welding systems that are connected, adaptive, and driven by data.New welding techniques aim to be eco-friendly and researchers are working to cut energy use and make resource use more efficient.
Conclusion
The history of welding exemplifies humanity's drive toward innovation, efficiency, and progress. Welding has come a long way. It started with the forge welding of Ancient Egypt. Now, it includes robotic automation and laser precision. This evolution meets society's needs and blends science, craftsmanship, and industry. Today, welding is an essential tool.WeldingSupply.com is dedicated to offering the latest welding products. As technology advances, we ensure that fabricators around the world can access the next chapter of welding history. Welding has a long history and remains vital today. Whether using old techniques or new technologies, it plays a key role in shaping the future.